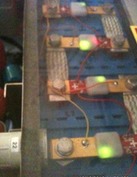
Every EV owner knows that the condition of their traction pack trumps everything. If its working well, the car is fine, if its playing up then you have problems.
Managing the traction pack is a first-order skill for any EV driver.
nov13
I always knew that the 45 batteries that make up my traction pack were a critical part of the 'engine' that drives my car. Sadly that didn't translate into intelligent action when I didn't heed (or even see) the BMS's Warning Light when it started coming on. A few months later I noticed that the car wasn't performing as well as it used to; and by that point I had caused some damage to the weakest batteries in the pack.
Someone once described what happens when the batteries get low, as a wolf pack turning on the weakest member, and that is certainly what happened here. Test drives with a quickly acquired CellLog 8S eight-cell voltage logger allowed me to prove what everyone else seemed to know, namely that I had undermined a significant number of individual batteries (see the Sag Ratio graph below).
Helpful guidance and advice from the AEVA community showed me how to graph and identify the cells, (including 'weber', who helped assemble the Sag Ratio, below) and hence we identified 10 cells to replace. Lithium Battery supplier Rod Dilkes from EV-Power.com.au quickly provided 10 batteries and recommended Chris Jones (also an AEVA-WA member and now our President) to install them.

Sag Ratio (or ability to avoid voltage drop) of all 45 cells, from best of 1.0 (Left) to poorest. Above 2.0 is poor. With the help of other data too, we decided to replace the rightmost 10 cells.
We arranged that Chris would do three things:
- replace the 10 worst cells, identified above (#s 17,45,36,5,25,4,10,27,1 & 26),
- also move the next few borderline cells from the bottom pack (#s 1-21), and
- leave only the best cells in the lower pack, which is harder to get to than the top pack (the pic below shows the top battery pack near the hinge when the engine cover is raised). Removing the bottom set isn't that hard, but it is a lot easier with a hoist and a extended jack. For the top pack , there is just a clear cover.
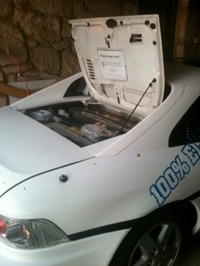
This means that 5 bad cells NOT underlined from the top pack were replaced and 5 in the lower pack (the underlined ones) were also replaced and finally the next weakest 5 cells (#s 21, 8, 14, 20, 11 and 16) were moved up. Thus all 10 new cells were placed below. As a result the weaker 19 out of 45 cells (or over 40%) were either replaced or made much more accessible.
So will that fix the problem? And how do I stop the problem recurring?
Subsequent events prove that the mix of batteries has indeed settled into a satisfactory working arrangement. Charging now goes off without a hitch - but not before a difficult week of settling down and occasional charging of individual cells - and the pack has returned to the previous 20%/hour to recharge plus the normal 'topping out' time at the end. Next, avoiding a recurrence centres around making the Battery Warning light more obvious. Even more important might be adjusting the Zilla controller so that the maximum current draw and allowed voltage drop are more restrained. This might be another blog entry...
In the meantime I have found a clever auto electrician (recommended by the guys at William Brown Autos, in fact) called Mark, at Automotive Electrical Designs who is going to move the BMS warning light into a more visible spot… Either smack bang at the top of the instrument console somewhere, or better still, use an existing light on the dash. I am hoping that the IGN light can be co-opted into the role.
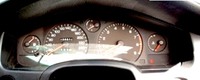
After all this is a potentially serious electrical problem, so what better light? And the old function of the IGN light is not so relevant anymore, as it used to indicate when the Alternator has stopped working. Now since we neither have an alternator nor does the new tiny 12V battery have to turn over a heavy petrol engine, it seems that the existing Battery Voltage Gauge (visible as a small dial, upper-middle of the instrument gauges) can provide enough monitoring.
What have I learned?
Well, I now have a six cell charger - so I can charge individual cells; and a CellLog 8S 8-cell voltage data logger. Thus I have the ability to charge and monitor every battery in the traction pack. These have been useful. Shortly the ZEV240 will have a much more robust way of drawing the driver's attention to the state of the traction pack via a conspicuous red light on the dash; and finally I have acquired the plugs and cables needed to adjust the Zilla' power configuration. Not sure yet what's involved, so if you have any suggestions, please say.I could argue I have learned a bit about the expense of maintaining the cells of a traction pack too, but we'll pass on that.
Will these proposals be enough? Are there other items I should have addressed to preserve the traction pack? What do you think?
Oh, and anyone want to buy 10 used Lithium cells, good for a UPS or other stationary task? :-))
bdc